Es war einmal ein Cobot
Die Entwicklung des Cobotmarktes: Eine Historie der kollaborativen Roboter
Einleitung
Kollaborative Roboter, oder Cobots, haben sich in den letzten zwei Jahrzehnten rasant entwickelt. Sie bieten eine Vielzahl von Möglichkeiten zur Zusammenarbeit zwischen Mensch und Maschine, insbesondere in der Fertigung und Automatisierung. Dieser Artikel beleuchtet die Geschichte und Entwicklung des Cobotmarktes, angefangen von den Anfängen mit wenigen Herstellern bis hin zu den heutigen, vielfältigen Marktangeboten und den Herausforderungen in Bezug auf Normen.
Die Anfänge der Cobots
Die ersten Kollaborationsroboter wurden in den frühen 1990er Jahren entwickelt. Pioniere wie Kiva Systems und Universal Robots (UR) legten damals den Grundstein für eine neue Ära der Robotik. Die Technologien waren jedoch noch in einem sehr frühen Stadium, und die Anwendungen waren begrenzt.
1996: Der erste Cobot, das „Robot Arm“ von Professor Harry Mak, wurde entwickelt. Diese Roboter waren darauf ausgelegt, sicher in der Nähe von Menschen zu operieren und einfache Aufgaben zu übernehmen.
2000er Jahre: Universal Robots (gegründet 2005) stellte 2008 den UR5 vor, der durch seine Flexibilität und Benutzerfreundlichkeit besticht und vielen Unternehmen den Einstieg in die Automatisierung mit Cobots erleichtert hat.
Herausforderungen und Normenlage
Ein wesentliches Hindernis in den frühen Jahren der Cobot-Entwicklung waren die uneinheitlichen Normen und Sicherheitsvorschriften. Der Mangel an klaren Richtlinien führte zu Unsicherheiten bei der Implementierung und Nutzung von Cobots.
Sicherheitsbedenken: Unternehmen waren besorgt, dass Cobots, die in direkter Zusammenarbeit mit Menschen operieren, zu Verletzungen führen könnten. Dies führte zu einer Skepsis gegenüber der Technologie.
UN-ISO-Normen: Die internationale Normenorganisation begann, sich mit dem Thema auseinanderzusetzen. Die Notwendigkeit für einheitliche Normen wurde zunehmend erkannt, um eine sichere und effiziente Entwicklung der Cobots zu gewährleisten.
Fortschritte in der Normierung
Ein entscheidender Schritt in der Entwicklung des Cobotmarktes war die Einführung spezifischer Normen. Ein Meilenstein war die Veröffentlichung der ISO/TS 15066 im Jahr 2016, die erstmals umfassende Sicherheitsrichtlinien für Cobots bereitstellte. Diese Norm definiert, unter welchen Bedingungen und wie Cobots sicher in Zusammenarbeit mit Menschen eingesetzt werden können.
Im Jahr 2025 wurde die ISO/TS 15066 nun in die aktualisierte ISO 10218-2:2025 integriert, was den Cobots eine noch breitere Akzeptanz und Standardisierung im Markt verschafft.
Der heutige Cobotmarkt
Heute ist der Markt für Cobots stark gewachsen, sowohl in der Anzahl der Hersteller als auch in der Vielfalt der angebotenen Produkte. Cobots sind jetzt in vielen Branchen anzutreffen, von der Automobilproduktion bis hin zur Elektronikfertigung, und bieten Unternehmen flexible Lösungen zur Automatisierung.
10 verbreiteste Cobot-Hersteller
Hier ist eine Liste der 10 bekanntesten Cobot-Hersteller weltweit:
Universal Robots – Pionier im Cobot-Bereich mit verschiedenen Modellen wie UR3, UR5 und UR10.
KUKA – Bekannt für ihre industriellen Roboter und Kollaborationslösungen.
Rethink Robotics – Hersteller des berühmten Cobot „Baxter“
FANUC – Bietet eine breite Palette von Robotern einschließlich Cobots.
Yaskawa – Hersteller von Industrierobotern, einschließlich Cobot-Lösungen.
ABB – Bietet verschiedene Cobot-Modelle, die für Zusammenarbeit mit Menschen ausgelegt sind.
Techman Robot – Kombiniert Roboterarm mit einer integrierten Kamera zur intelligenten Automatisierung.
Doosan Robotics – Südkoreanischer Hersteller von Cobots, bekannt für Benutzerfreundlichkeit und Sicherheit.
Denso Robotics – Bietet Cobots mit Fokus auf Effizienz.
Nachi-Fujikoshi – Umfasst robuste und sichere Cobot-Optionen.
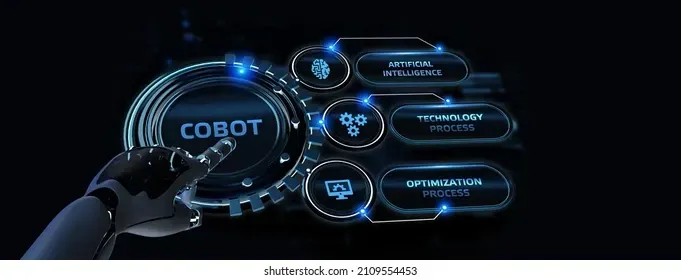